EkaPress follows a systematic approach to diagnose and repair equipment. Here are the steps that the company takes to ensure that equipment is fixed efficiently and accurately:
- Initial Assessment: The first step in diagnosing equipment issues is to conduct an initial assessment. This involves inspecting the equipment and identifying any visible signs of damage or malfunction. The technician may also ask questions about the equipment’s usage and history to gain a better understanding of the issue.
- Diagnostic Testing: EkaPress uses advanced diagnostic tools to identify the root cause of the equipment issue accurately. These tools help technicians identify specific problem areas and determine the best course of action for repair.
- Repair Plan: Based on the initial assessment and diagnostic testing, EkaPress creates a custo
mized repair plan tailored to the equipment’s specific needs. The repair plan includes an estimate of the time and cost required for the repair, along with any replacement parts needed.

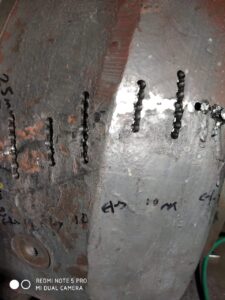
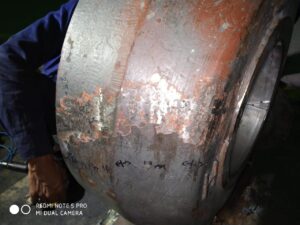
4. Repair and Maintenance: EkaPress’s skilled technicians execute the repair plan using the latest tools and technology. They perform the necessary maintenance tasks, including cleaning, lubrication, and adjustment, to ensure that the equipment is functioning correctly.5. Quality Assurance: Once the repair and maintenance work is completed, EkaPress conducts quality assurance testing to ensure that the equipment is operating correctly. This includes a final inspection of the equipment to verify that it meets the necessary safety standards and industry regulations.
6.Follow-up and Maintenance Plan: EkaPress provides a follow-up maintenance plan that includes routine maintenance tasks to ensure that the equipment continues to operate efficiently. The maintenance plan includes regular inspections, cleaning, and other maintenance tasks to prevent future breakdowns and ensure that the equipment operates smoothly.
To know more info please visit our official website: